Project Details
Our client produces a range of tableted medicines from its manufacturing plant in the south of Ireland. Due to its diverse range of products, regular cleaning cycles of the processing equipment are required, and the efficiency of this cleaning cycle is crucial to maintaining the highest quality standards of their products. The introduction of new processing equipment in the plant prompted the need for a new range of wash racks to hold the processing equipment in place during its cleaning cycle.
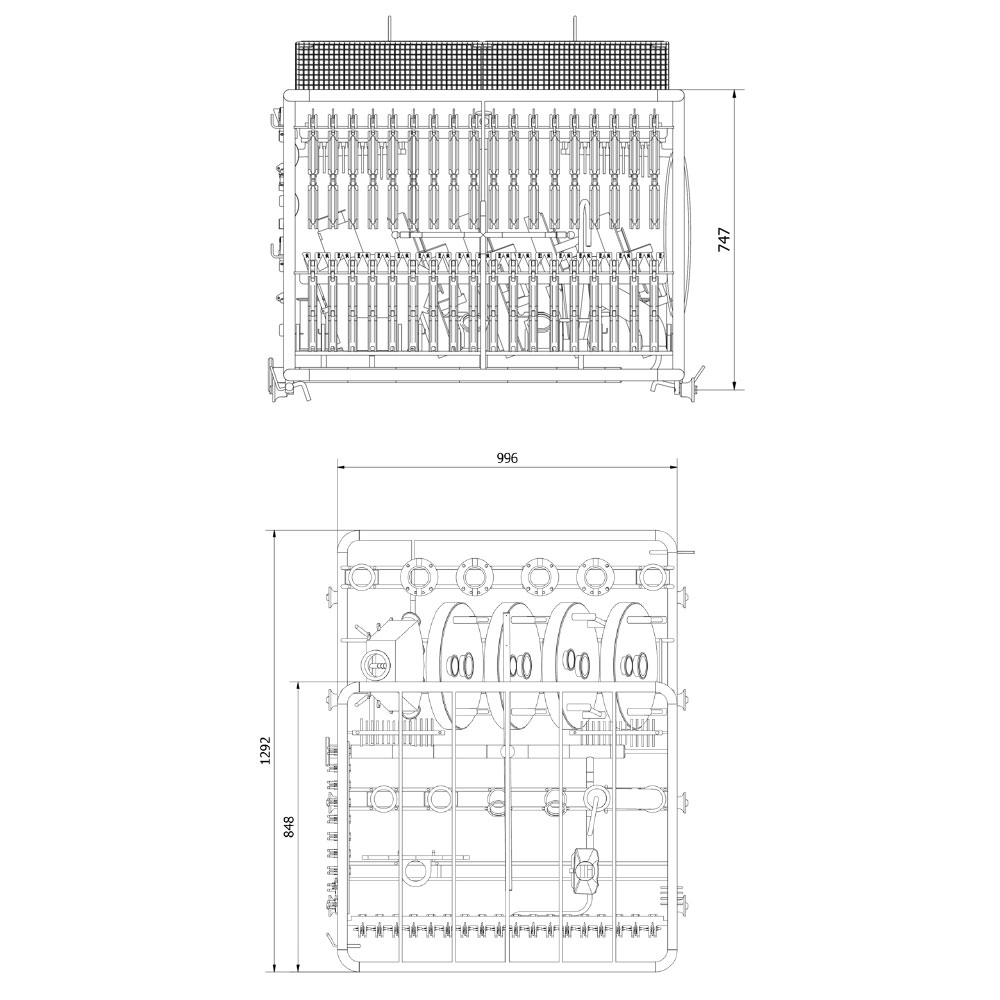
Wash rack system plan.
The introduction of new processing equipment which needs to be washed between production batches comes with a wide range of associated ancillary equipment. In previous years, we were tasked with the manufacture of both exact copies of existing wash racks, and the design and manufacture of bespoke wash racks to suit new equipment. Transport trollies and storage racking for these wash racks were also a substantial part of the work required.
Our approach to successfully completing this project was very exact. For duplication of existing racks, we relied on our metrology grade 3D hand scanner to capture an exact digital copy of the existing rack. This allowed us to overlay a solid model of the rack in preparation for in-house fabrication. A similar process was followed to create the bespoke designed racks. Using the same 3D hand scanner, we scanned the actual parts that were required on each of the racks to allow us to virtually load the racks using 3D design software. Following the scanning, we worked closely with our client’s operations team to group parts on each rack to align with the assembly sequence of the machine, ensuring parts could be disassembled and reassembled from the machine directly from the rack.
Five bespoke-designed wash racks, three identical copies of existing racks, five transport trollies and four storage racks were delivered to site well in advance of our client’s commissioning date. A strict site acceptance test (SAT) was performed by our client including the swabbing of all washed parts post SAT wash cycle for the presence of uncleaned residue. All parts delivered a clear pass result allowing fast progression of the equipment into the production cycle. A full Engineering Turnover Package was submitted with each item ensuring full traceability of each piece of equipment.